Among the finalists: Saarbrücken students secure the assembly of airplanes with artificial intelligence
They are the only German team among the seven finalists Airbus has selected to “shape the future of aviation”: Three young researchers from Saarland University want to make aircraft production safer and lighter. They have developed a system that uses artificial intelligence during assembly to ensure that the rivets, i.e. metal pins connecting the aircraft components, are absolutely secure. With their idea they prevailed against 269 teams of 284 universities from 72 countries. The final round will take place in Toulouse today. With the “Fly Your Ideas” competition, Airbus and UNESCO called on students worldwide to develop ideas for the future of aviation and space travel.
Hundreds of thousands, or depending on size even up to several million small metal bolts in an aircraft ensure that the individual components are held together. Even if each rivet weighs only a few grams, they all add up to a lot of weight and high production costs. The components are pre-drilled, laid on top of each other, and an assembler places the rivet, which has a thicker setting head at one end similar to a nail. A second fitter holds the rivet on the other side with an anvil. A few blows with a riveting hammer – and on the anvil the protruding rivet end is flattened into a closing head. If the rivet fits correctly, the components are firmly connected and can withstand the strongest loads and the most adverse conditions.
But mistakes can also happen: “Particularly in places that are difficult to access, it can happen that the rivet does not meet the tolerance specifications for width and height, for example, because the fitter does not position the anvil at the right angle or the rivet hammer slips slightly from the outside fitter. Or the rivet may splinter due to incorrect pre-treatment,” explains Tobias Masiak. He studied mechatronics at the Technical University Mittelhessen in Friedberg and is now doing research for his doctoral thesis at the Chair for Assembly Systems of Professor Rainer Müller and at the Saarbrücken Center for Mechatronics and Automation Technology (ZeMA), which Müller heads.
“The aircraft manufacturers check at safety-critical points whether the rivets are within the tolerance range and are firmly and correctly seated. But with so many, it’s simply impossible today to check them all,” says the doctoral student. The aviation industry therefore follows the motto “a lot helps a lot”: they play it safe and place more rivets than would be necessary, which experts aptly call fearless rivets. “They not only increase material and assembly costs, but also weight, fuel consumption and environmental impact,” says Masiak.
In a team with computer science students Aditya Gulati and Daniel Gusenburger, he wants to find a remedy. With their project “AIQ-Inspect” (short for: Artificial Intelligence Quality Inspection), they are taking part in the Airbus “Fly Your Ideas” competition. “Professor Müller and his research group are working on projects aimed at supporting aircraft fitters in riveting. This gave rise to the idea of collecting data on the riveting process and using artificial intelligence to teach a system so that the fitter can immediately tell whether the rivet is correctly seated or not by wearing data goggles,” explains Masiak.
This would enable quality control for precise manual work directly during assembly, “on the fly” as it were. For their system, the junior researchers rely on research work, the robot system and the sensor technology at ZeMA and the chair. They combine three sensors that keep a close eye on the riveting process: A laser line sensor monitors the width and height of the rivet closing head by means of a 3D point cloud, a force-torque sensor measures the forces acting during the riveting process and checks whether the rivet is correctly positioned, and a camera takes a picture at the appropriate time. With this setup, the students monitored the riveting process, hammering hundreds of rivets into metal plates littered with holes that match aircraft components in material and thickness. Using this data, they used machine learning methods and artificial intelligence to teach their system how to reliably detect whether the rivet is seated or not during the work process. Using data glasses, the system gives the hammering fitter feedback: green for “properly seated”, red for “failing”. And this can also be checked remotely online.
The team from Saarland University initially made it to the second round with 50 of the 270 groups participating in the competition. Experts then chose AIQ-Inspect to participate in the final round, along with two teams from Cambridge and one each from the University of Strathclyde in the UK, the Delft University of Technology in the Netherlands, the Polytechnic University of Milan (Italy) and the National University of La Plata (Argentina). The winners will have the chance to further develop their idea in the aerospace industry.
Further Information:
https://www.airbus.com/newsroom/press-releases/en/2019/04/airbus-selects-seven-finalist-teams-to-shape-the-future-of-aerospace.html
https://twitter.com/AiqInspectors
Questions can be directed to:
Tobias Masiak
Zentrum für Mechatronik und Automatisierungstechnik (ZeMA)
Tel.: +49 68185787 – 581
E-Mail: t.masiak@zema.de
Die Öffentlichkeitsarbeit am Saarland Informatics Campus wird unterstützt durch das Kompetenzzentrum Informatik Saarland, gefördert aus Mitteln des Europäischen Fonds für regionale Entwicklung (EFRE) und Mitteln der Staatskanzlei Saarland.
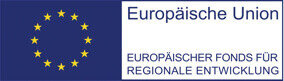
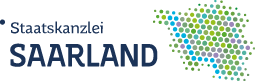